SkyCube iQ
Leave the intelligent booking decisions to us, and you can get the optimal loading plan for maximum benefits.
Charter and Booking Better with Redoubled Power
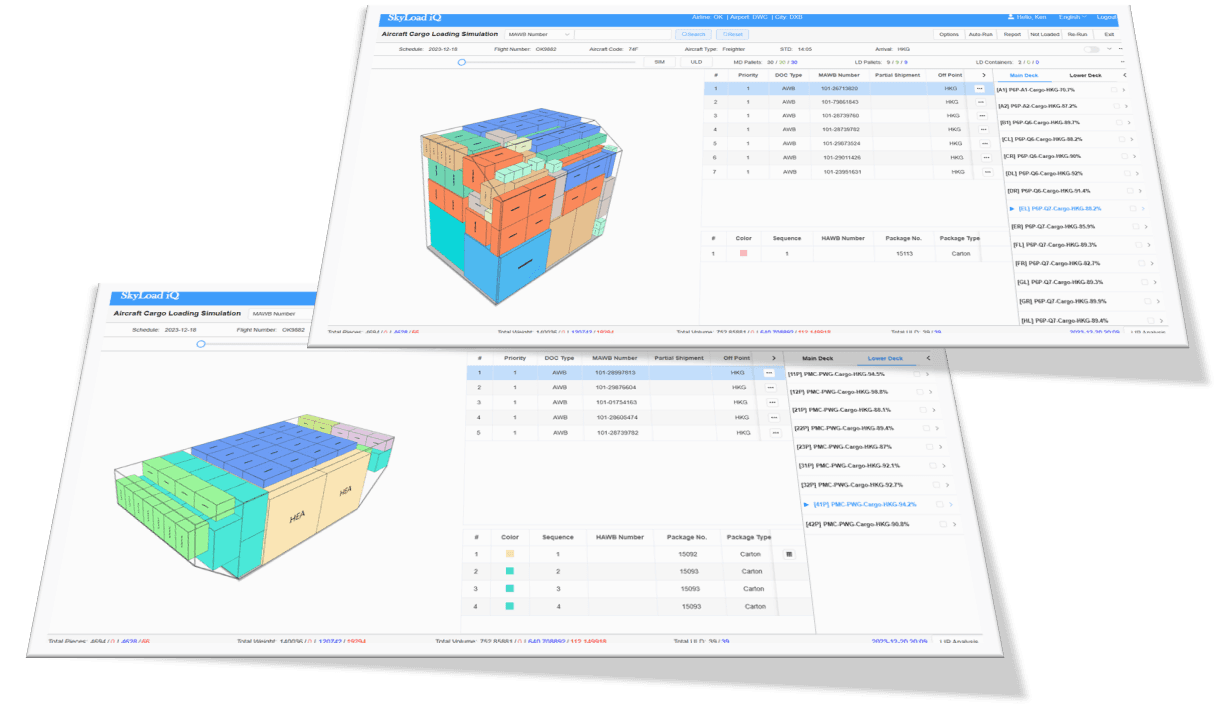
Auto Interlocking
The intelligent computation engine automatically assesses the dimensions and shapes of each item, selecting the most suitable interlocking mode (Block, Brick, Pinwheel) to achieve an optimal stacking arrangement. This enhances stability and compactness, minimizing gaps between items and maximizing the utilization of pallet space.
Load by Block Stacking(PMC-LDP)
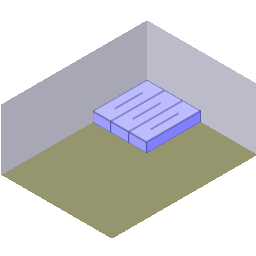
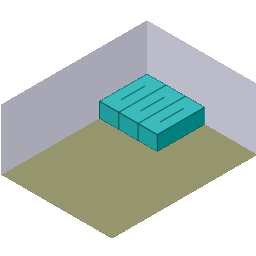
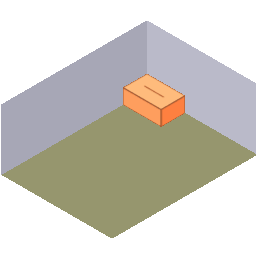
Load by Pinwheel Stacking (PMC-LDP)
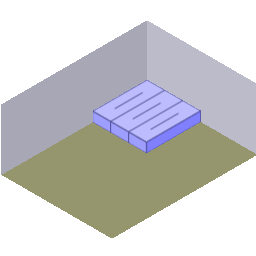
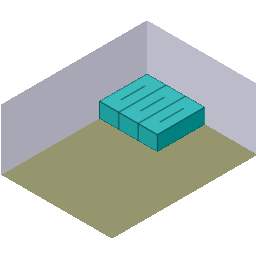
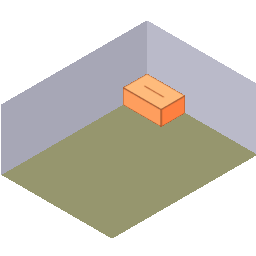
Auto Overhang Loading
For the lower cargo compartment, in order to effectively utilize the space, and to meet the special loading requirements for long-sized cargo, an intelligent computing engine will automatically calculate the required elevation for overhanging shipments based on factors such as the dimensions, weight, and balance of the cargo. This ensures the rationality and stability of the loading process, effectively utilizing space in each position.
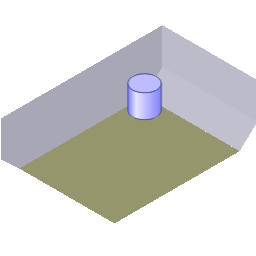
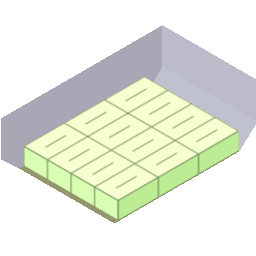
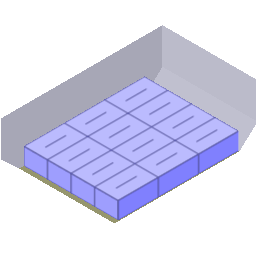
Meet SkyCube iQ
The restrictions on cargo loading and stacking refer to the limitations and regulations that must be followed when stacking cargo inside ULDs. To ensure the safety of the flight, loaded cargo should be stacked and secured correctly, ensuring stability and preventing movement or sliding during flight, which could disrupt the balance of the aircraft. The following is an overview of the functions related to the shipments stacking:
ULD Loading Direction
In the process of ULD build up, it is common to select the appropriate stacking orientation based on the characteristics and dimensions of the cargo. Simultaneously, consideration must be given to the capacity and stability of the ULD to ensure that the cargo does not tilt or get damaged during the loading process. In cases of mixed loading, a flexible approach involving both back-to-front or bottom-to-up stacking is employed to maximize the utilization of ULD space while ensuring the safe transportation of the shipments.
Optimization Over Multiple ULDs
With the assistance of the smart optimization engine, it automatically analyzes the characteristics, dimensions, and weight of various shipments. The system intelligently selects the most suitable combination and quantity of ULD types based on destination and cargo type, maximizing loading space utilization. This enhances efficiency and optimizes ULD loading in air cargo transportation.
Possible Package Orientation Rules
For shipments of different packaging types, corresponding rotation direction constraints can be freely and flexibly set to meet space utilization, cargo safety, and operational requirements. It supports complex wrapping rotation conditions and can simultaneously consider constraints such as horizontal rotation, length flipping, and width flipping. Fully automated intelligent loading calculations ensure that the rotated shipment can maximize space utilization, avoiding space wastage or overly compact stacking. At the same time, it also ensures that the stacking of shipments does not affect their stability and safety, preventing incidents such as shipment tipping or damage.
Packages Stacking Shrink Height
Considering the shrink height that occurs when stacking a shipment on top of each other is of utmost importance, especially for certain types of goods that are susceptible to compression, such as paper products, chemicals, and food items. The optimization engine takes into account the weight on the upper layers during stacking , thereby minimizing the decrease in height of the lower layers and ensuring that the stacking process does not result in damage or compromise the quality of the goods. Meanwhile, the overall balance and safety of the stacking process must also be considered to ensure the smooth execution of loading operations.
Partial Loading and Re-Loading
Re-Loading refers to the process of adding additional shipments to a ULD after it has already been loaded with shipments. This is done when there is still available space within the ULD. The purpose of re-loading is to maximize the use of the ULD's available space without altering the initial loading plan. Re-loading calculations are performed to determine the quantity and placement of additional shipments based on the remaining space within the ULD. This process improves loading efficiency and minimizes wasted space while maintaining the integrity of the originally scheduled shipments arrangement.
Container Door Size Restrictions
For the container loading operations, it is necessary to compare the dimensions of the shipment with those of the container doors. While the dimensions of the goods may fit into the container, if they exceed the size of the container doors, the smart optimization engine will decide not to load and will automatically search for alternative ULD loading, thereby enhancing the accuracy and safety of the loading process. This allows operators to promptly understand the loading situation, ensuring that the loading of shipments complies with the requirements.
Shipments of the Same Grouping Loaded Together
In the loading plan, it is possible to designate each different shipments as the same group, with the aim of loading them together in the same ULD whenever possible. To meet the requirements of ULD build up, the shipments belonging to the same group is automatically loaded into the same ULD, reducing the number of loading and unloading operations and optimizing the loading of shipments in the same group. This enhances loading efficiency and accuracy.
Mixed Loading
Loading a combination of cylindrical and cubic shipment presents a challenging technical endeavor, as these two distinct shapes may necessitate different handling approaches during loading to ensure there is no mutual compression between cylindrical and cubic items. Leveraging a fully automated intelligent computation engine, this process takes into account spatial optimization during stacking, strategically arranging the placement of cylindrical and cubic shipments to maximize loading space utilization.
Loading Sequence
Designating the loading sequence for shipments refers to the ability to freely specify the loading and unloading order of goods during the loading process. This ensures that, upon unloading at the destination or transfer point, the shipment is efficiently unloaded in accordance with its designated order, facilitating sorting operations.